I haven't been posting much here, but I've been making a lot of stuff! Here's where you can find my current projects
Facebook: https://www.facebook.com/chickenprops/
Instagram: https://www.instagram.com/jasperjandersonfx/
Incidentally, the main reason I haven't been updating the blog is that Facebook blocks links to here as spam, so if anyone has any suggestions on how to fix that, let me know.
Friday, July 3, 2020
Tuesday, November 13, 2018
The Ring of Dracula
The Universal Monsters have always been a big influence on me, and I started thinking recently about putting together a little display of a few of the smaller pieces from those films. The Wolf Man has a silver wolf's head cane, Dracula and the Mummy both have themed rings, and the Frankenstein Monster's equivalent piece of jewelry is... the neck electrodes! So this should be a fun little diversion project.
I decided to start with the Dracula crest ring. There have been a few replicas produced over the years, and they all look nice at a glance, but once I saw the auction photos of the original ring, which belonged to Forry Ackerman for many years, it became clear that most of the current replicas are very sterilized, geometric interpretations of what would have been an organic, hand sculpted design, presumably by a jeweler in the '40s. Yes, the 1940s. In the original Dracula film in 1931, Lugosi wore a plainer ring. This more extravagant Dracula crest ring was first seen in the John Carradine sequels (though was probably altered from the Lon Chaney Jr. Dracula/Alucard ring), and finally worn by Lugosi in Abbott and Costello Meet Frankenstein.
There have also been replicas molded from the original ring, but they seemed to suffer from lost detail. You'll see the original in the printouts I'm working with for my rendition.
Anyway, detailed though it is, I thought I would be able to sculpt the ring in Apoxie Sculpt, and if I mixed in aluminum powder, it would be able to be buffed to a metallic shine. I did several tests with several methods, but didn't come up with something that would be workable at the fine level of detail I would need. So I decided to use Super Sculpey Firm, because it is hard enough to hold the sharp detail, and could be sanded after baking if needed. I jumped right in to the crest. I scaled the auction photos to full size, and cut out templates to help keep my proportions correct. I also traced the image onto a piece of clear plastic, so I could hold it over the sculpture to check. I ended up using various sizes of needles as my loop tools! Once that was baked and cleaned up a bit, I dumped some silicone on it. I cold cast it the way that's worked best for me in the past, which is to coat the surface with metal powder, and fill with black resin. Buff with steel wool, a very slight black wash, and the crest is done.
I had to think quite a bit about how I would mold the main ring part before proceeding. The thing about cold casting is it's very difficult to repair any imperfections in the seam or otherwise, because you need to preserve that ultra thin surface layer of metal. Once I figured out that I could have a removable dowel in the center, and split the mold where the band joins the main hunk of material, I could start sculpting. I decided that I would not attempt to mount a separate stone of any sort in the center. The tolerances would have to be so precise that it wasn't going to be worth it. Instead, I'd just sculpt it right in, and paint it later. The center of the stone would actually be the perfect place for a pour spout, since the crest would cover it up.
I decided to start with the Dracula crest ring. There have been a few replicas produced over the years, and they all look nice at a glance, but once I saw the auction photos of the original ring, which belonged to Forry Ackerman for many years, it became clear that most of the current replicas are very sterilized, geometric interpretations of what would have been an organic, hand sculpted design, presumably by a jeweler in the '40s. Yes, the 1940s. In the original Dracula film in 1931, Lugosi wore a plainer ring. This more extravagant Dracula crest ring was first seen in the John Carradine sequels (though was probably altered from the Lon Chaney Jr. Dracula/Alucard ring), and finally worn by Lugosi in Abbott and Costello Meet Frankenstein.
There have also been replicas molded from the original ring, but they seemed to suffer from lost detail. You'll see the original in the printouts I'm working with for my rendition.
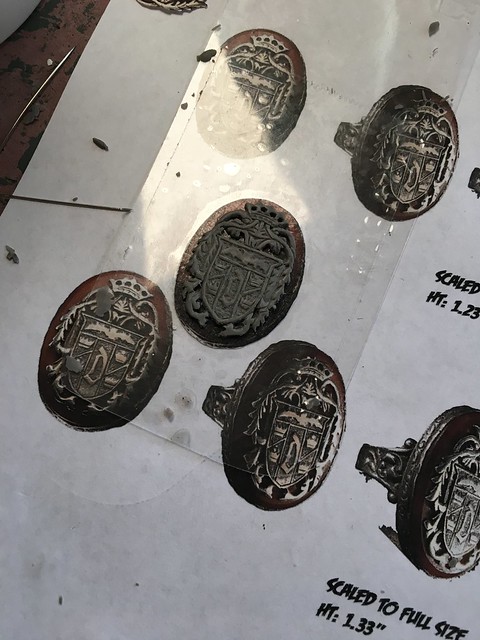
Anyway, detailed though it is, I thought I would be able to sculpt the ring in Apoxie Sculpt, and if I mixed in aluminum powder, it would be able to be buffed to a metallic shine. I did several tests with several methods, but didn't come up with something that would be workable at the fine level of detail I would need. So I decided to use Super Sculpey Firm, because it is hard enough to hold the sharp detail, and could be sanded after baking if needed. I jumped right in to the crest. I scaled the auction photos to full size, and cut out templates to help keep my proportions correct. I also traced the image onto a piece of clear plastic, so I could hold it over the sculpture to check. I ended up using various sizes of needles as my loop tools! Once that was baked and cleaned up a bit, I dumped some silicone on it. I cold cast it the way that's worked best for me in the past, which is to coat the surface with metal powder, and fill with black resin. Buff with steel wool, a very slight black wash, and the crest is done.
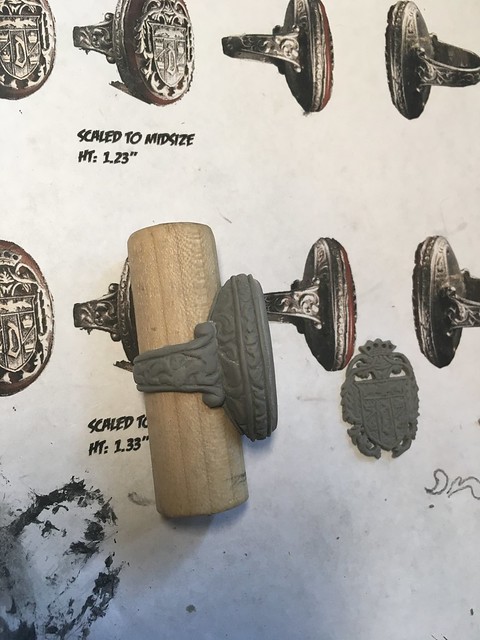
I had to think quite a bit about how I would mold the main ring part before proceeding. The thing about cold casting is it's very difficult to repair any imperfections in the seam or otherwise, because you need to preserve that ultra thin surface layer of metal. Once I figured out that I could have a removable dowel in the center, and split the mold where the band joins the main hunk of material, I could start sculpting. I decided that I would not attempt to mount a separate stone of any sort in the center. The tolerances would have to be so precise that it wasn't going to be worth it. Instead, I'd just sculpt it right in, and paint it later. The center of the stone would actually be the perfect place for a pour spout, since the crest would cover it up.
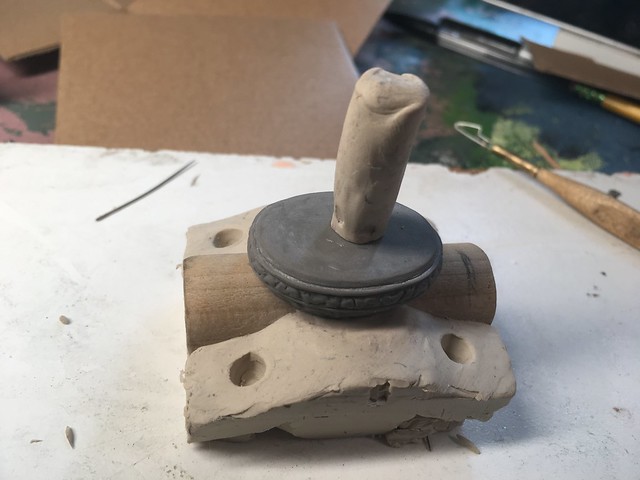
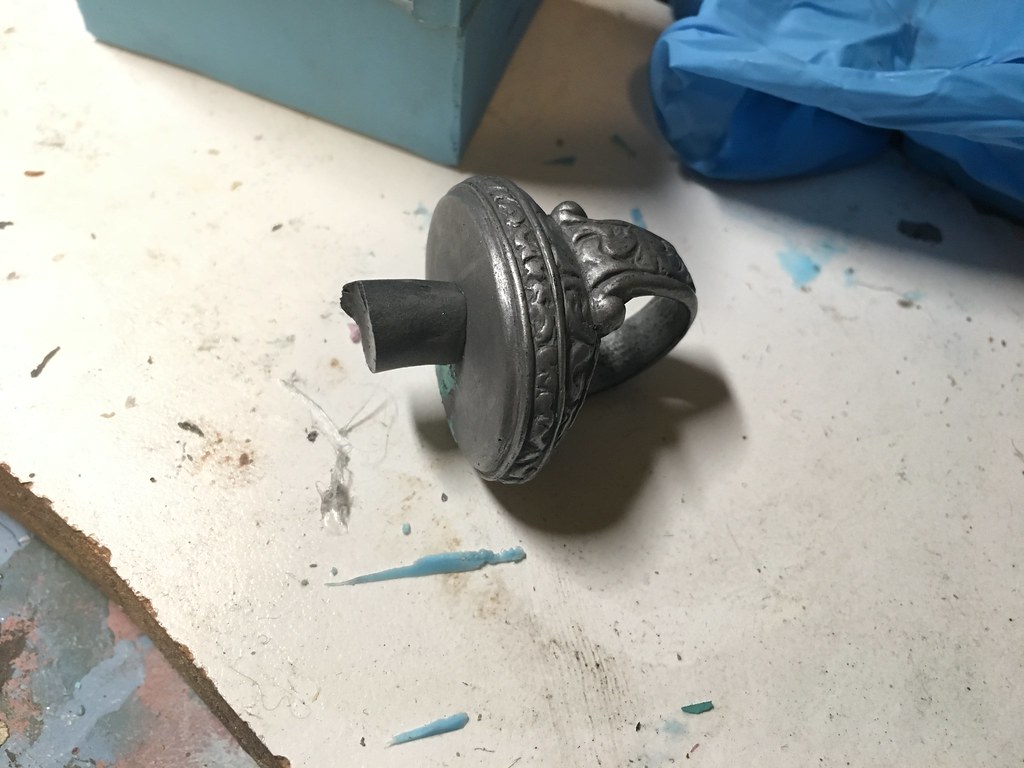

Sculpt, mold, cast the same way. I released the dowel with vaseline, and coated it in aluminum powder. It didn't quite take to the resin like the metal on the silicone sections did, but it's on the inside, so it doesn't matter much. With the stone painted, and a black wash over the recesses, I could carefully superglue the crest on top. And that's not too shabby for a plastic recreation. It's not perfect. I think I'd need some smaller needles to really get a 100% match on the sculpture, but I think it captures the feeling of the original. I gained a lot of respect for old school wax jewelry sculptors, too.
More to come!
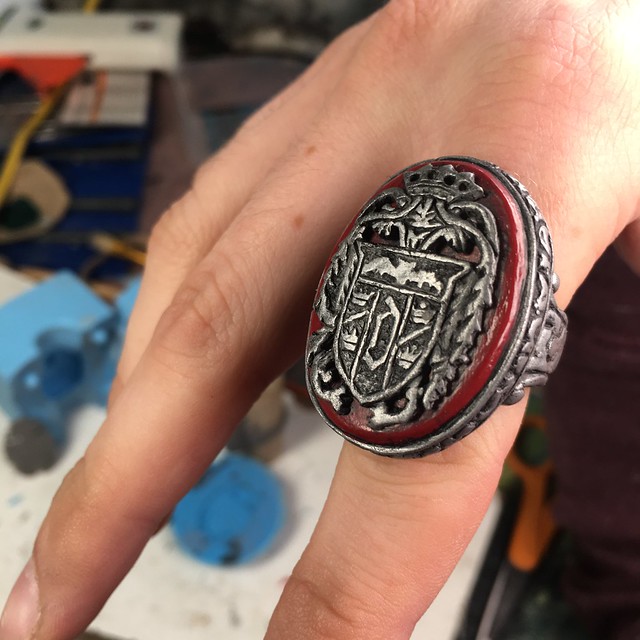
More to come!
Monday, October 29, 2018
You Seem a Decent Fellow. I Hate to Kill You.

Our Princess Bride costumes made the rounds this past weekend. Here are a few brief notes on how we did it...
Inigo Montoya:
-found a shirt, dyed and added leather laces
-vest made from scratch with faux leather
-boots are women's boots with added faux leather cuffs
-wig was a cheap number, cut and styled, but set it back on my head to use my own hair as bangs
-mustaches are from Frends Beauty, trimmed
-pants were also used for Han Solo a few years ago
-belt is a "close enough"
-scars are 3rd Degree silicone

Dread Pirate Roberts:
-mask is a vacuum form of her face with faux stretch leather glued on top and an elastic band
-bandana and sash were just lengths of black fabric, hemmed
-added faux leather boot tops to regular boots
-cheap $7 frogs used for both swords
-bought a basic black pirate shirt. The sleeves aren't as full, but it's all so darned black that you can't really perceive whether the details are right
-her own pants and belt.

Inigo Montoya:
-found a shirt, dyed and added leather laces
-vest made from scratch with faux leather
-boots are women's boots with added faux leather cuffs
-wig was a cheap number, cut and styled, but set it back on my head to use my own hair as bangs
-mustaches are from Frends Beauty, trimmed
-pants were also used for Han Solo a few years ago
-belt is a "close enough"
-scars are 3rd Degree silicone

Dread Pirate Roberts:
-mask is a vacuum form of her face with faux stretch leather glued on top and an elastic band
-bandana and sash were just lengths of black fabric, hemmed
-added faux leather boot tops to regular boots
-cheap $7 frogs used for both swords
-bought a basic black pirate shirt. The sleeves aren't as full, but it's all so darned black that you can't really perceive whether the details are right
-her own pants and belt.

Sunday, October 21, 2018
One Sword, Two Sword
Mrs. Chicken and I have been working on our Hallowen costumes for some time now. I'll say the theme is The Princess Bride, and you'll probably figure it out pretty quickly, but before the big reveal, I wanted to do a specific post on one of the most important and complicated parts of the outfits: the swords.
First, we needed Inigo Montoya's sword. Gold, jewel-encrusted, and ornate, it has a very specific look. I don't think you could do the costume justice without getting reasonably in the ballpark. I spent a long time looking for an existing replica, or a "close-enough" product. I looked at many a swept hilt rapier, but nothing even had the general shape of the hilt.
Then I saw that IndyMagnoli on the RPF is in the process of doing a run of beautiful reproductions of the Inigo sword, but they won’t be ready in time for Halloween, so it was back to doing things the old fashioned way. And I mean that in a general sense, because I had never made something quite this way before.
I thought about making a blade, but the thought of all that grinding of metal was giving me a headache, so I found a cheap rapier for $40 on Amazon to cannibalize.
On studying the construction of what looks like a very complicated, swirly, twisty hilt, I determined that it would be impractical to mold as one piece, or even a few pieces, especially given also the fact that I only needed one. Really, the way the original maker probably made the hilt is out of a few flat pieces bent and fused together. I could take a similar approach with plastic. Cue the 3D printer. I mocked up the concept in paper to be sure it would work.
I am not a skilled 3D modeler, so I drew out a rough approximation of the intricate details of the guard in sharpie, following the outline I had prototyped in paper. Then I scanned those drawings, and used the tracing tools in Illustrator to turn it into vector outlines. That file could then be imported into a 3D modeling program (I used one of the free ones from Autodesk...123 something), and extruded into one thickness for the main body, and again a little taller for the details. Print two of everything, mirrored for the other side of the sword.
I printed in ABS, because it’s a bit stronger. Solid infill for extra strength. The thinking here was that if I printed the curved parts in a curve, the layers would be aligned to create weak points where it would snap through the thin bars. If I print it flat, one layer of plastic goes continuously around the whole surface, making for a stronger part. Then it's just a matter of hitting the parts with a heat gun, and shaping them to fit together.
A bit of acetone will bond the reversed ABS parts to each other, and will also seal in the outside, and melt it down a bit. I also rounded over the edges and some of the detail with a dremel sanding drum at this point. It could have been done in the model, but I was pleased with the way this worked out.
My mistake that I realized at this point was that the middle Y shaped piece should have been a bit larger. Oops.
I used a thick 5 minute epoxy gel to fuse the larger curved parts to the main guard, and to fill in the volume there. This stuff retains some flex when it cures, which means it’s less likely to break off at the join than if I had used a totally rigid glue.
I did another pass of acetone, but it wasn’t giving me the total smoothness that I wanted, so I went for a product that I really don’t like to use. Smooth On XTC 3D. It’s designed to be brushed on to 3D prints to clean up the layer lines, but it tends to obliterate all detail, too. It often goes on unevenly, and it’s an especially stinky epoxy. Not my top pick. But all of those usual drawbacks (except the stench) will actually work in my favor here, and give me a high gloss surface to do my faux chrome. So I slathered on a couple of coats.
Some Alclad Chrome paint, then a candy coat of orange makes a decent faux gold.
I decided to keep the original pommel because the weight of real metal is needed to make the sword balance properly in your hand. The shape was in the ballpark, too, which is one of the reasons I picked this donor sword originally. So then I just had to make a handle to fit between the pommel and the guard. I checked the size with a bit of 1/2” pvc pipe, and ended up using that as a base, onto which I added Freeform Air (leftover from a previous project). I figured out this time that using baby powder to smooth it was a cleaner way to go than alcohol.
I let that cure, then painted it and gave it a good wire wrap. Not too bad for $50 and some leftover materials.
The Dread Pirate Roberts sword was the next puzzle. I should mention that Factory Entertainment did both swords several years ago in a very small edition. I looked for these, but they’re long sold out, and it doesn’t seem like anyone who has one is parting with theirs. However, I spotted on Amazon what appears to be the manufacturer’s attempt to make a genericized version of the Dread Pirate Roberts sword. It’s the same guard, same handle, but a different pommel and a black blade.
They call it the Black Marauder Rapier. I can work with that. Frankly, this was the sword that could have been pretty generic. Most people wouldn’t know he difference no matter what sword he was holding, but where’s the fun in that?
The blade was blackened, and through some research, I found that you can just scrub it with vinegar and the blackening comes off. Give it a polish with some stuff made for stainless steel kitchen surfaces, and you've got a silver blade again.
The wrong pommel screws right off, so it would be easy to replace. And I had great reference of the correct pommel, due to the previous licensed replica. The bummer is that the swirling seashell design is a pain to 3D model. Yes, I’ll be printing this one, too. One thing the printer does much better than I do is geometry.
I got it modeled and printed hollow, with a receptacle for an appropriate hex nut. And then I filled the void with lead shot, backed with epoxy.
Sand, sand, sand the pommel. Then I gave the guard and the pommel a coat of gloss black enamel and the Alclad chrome treatment. I'm really impressed with how effective the chrome is on this. There's a little ring of metal at the top of the leather wrapped handle. I opted for aluminum tape on this part, rather than masking and painting, and it blends right in.
If you'd like to make your own swords, I've uploaded the files I made to Thingiverse.
Here's the Dread Pirate Roberts Pommel: https://www.thingiverse.com/thing:3114815
And here's the Inigo Montoya guard: https://www.thingiverse.com/thing:3054622
First, we needed Inigo Montoya's sword. Gold, jewel-encrusted, and ornate, it has a very specific look. I don't think you could do the costume justice without getting reasonably in the ballpark. I spent a long time looking for an existing replica, or a "close-enough" product. I looked at many a swept hilt rapier, but nothing even had the general shape of the hilt.
Then I saw that IndyMagnoli on the RPF is in the process of doing a run of beautiful reproductions of the Inigo sword, but they won’t be ready in time for Halloween, so it was back to doing things the old fashioned way. And I mean that in a general sense, because I had never made something quite this way before.
I thought about making a blade, but the thought of all that grinding of metal was giving me a headache, so I found a cheap rapier for $40 on Amazon to cannibalize.
On studying the construction of what looks like a very complicated, swirly, twisty hilt, I determined that it would be impractical to mold as one piece, or even a few pieces, especially given also the fact that I only needed one. Really, the way the original maker probably made the hilt is out of a few flat pieces bent and fused together. I could take a similar approach with plastic. Cue the 3D printer. I mocked up the concept in paper to be sure it would work.
I am not a skilled 3D modeler, so I drew out a rough approximation of the intricate details of the guard in sharpie, following the outline I had prototyped in paper. Then I scanned those drawings, and used the tracing tools in Illustrator to turn it into vector outlines. That file could then be imported into a 3D modeling program (I used one of the free ones from Autodesk...123 something), and extruded into one thickness for the main body, and again a little taller for the details. Print two of everything, mirrored for the other side of the sword.
I printed in ABS, because it’s a bit stronger. Solid infill for extra strength. The thinking here was that if I printed the curved parts in a curve, the layers would be aligned to create weak points where it would snap through the thin bars. If I print it flat, one layer of plastic goes continuously around the whole surface, making for a stronger part. Then it's just a matter of hitting the parts with a heat gun, and shaping them to fit together.
A bit of acetone will bond the reversed ABS parts to each other, and will also seal in the outside, and melt it down a bit. I also rounded over the edges and some of the detail with a dremel sanding drum at this point. It could have been done in the model, but I was pleased with the way this worked out.
My mistake that I realized at this point was that the middle Y shaped piece should have been a bit larger. Oops.
I used a thick 5 minute epoxy gel to fuse the larger curved parts to the main guard, and to fill in the volume there. This stuff retains some flex when it cures, which means it’s less likely to break off at the join than if I had used a totally rigid glue.
I did another pass of acetone, but it wasn’t giving me the total smoothness that I wanted, so I went for a product that I really don’t like to use. Smooth On XTC 3D. It’s designed to be brushed on to 3D prints to clean up the layer lines, but it tends to obliterate all detail, too. It often goes on unevenly, and it’s an especially stinky epoxy. Not my top pick. But all of those usual drawbacks (except the stench) will actually work in my favor here, and give me a high gloss surface to do my faux chrome. So I slathered on a couple of coats.
Some Alclad Chrome paint, then a candy coat of orange makes a decent faux gold.
I decided to keep the original pommel because the weight of real metal is needed to make the sword balance properly in your hand. The shape was in the ballpark, too, which is one of the reasons I picked this donor sword originally. So then I just had to make a handle to fit between the pommel and the guard. I checked the size with a bit of 1/2” pvc pipe, and ended up using that as a base, onto which I added Freeform Air (leftover from a previous project). I figured out this time that using baby powder to smooth it was a cleaner way to go than alcohol.
I let that cure, then painted it and gave it a good wire wrap. Not too bad for $50 and some leftover materials.
The Dread Pirate Roberts sword was the next puzzle. I should mention that Factory Entertainment did both swords several years ago in a very small edition. I looked for these, but they’re long sold out, and it doesn’t seem like anyone who has one is parting with theirs. However, I spotted on Amazon what appears to be the manufacturer’s attempt to make a genericized version of the Dread Pirate Roberts sword. It’s the same guard, same handle, but a different pommel and a black blade.
They call it the Black Marauder Rapier. I can work with that. Frankly, this was the sword that could have been pretty generic. Most people wouldn’t know he difference no matter what sword he was holding, but where’s the fun in that?
The blade was blackened, and through some research, I found that you can just scrub it with vinegar and the blackening comes off. Give it a polish with some stuff made for stainless steel kitchen surfaces, and you've got a silver blade again.
The wrong pommel screws right off, so it would be easy to replace. And I had great reference of the correct pommel, due to the previous licensed replica. The bummer is that the swirling seashell design is a pain to 3D model. Yes, I’ll be printing this one, too. One thing the printer does much better than I do is geometry.
I got it modeled and printed hollow, with a receptacle for an appropriate hex nut. And then I filled the void with lead shot, backed with epoxy.
Sand, sand, sand the pommel. Then I gave the guard and the pommel a coat of gloss black enamel and the Alclad chrome treatment. I'm really impressed with how effective the chrome is on this. There's a little ring of metal at the top of the leather wrapped handle. I opted for aluminum tape on this part, rather than masking and painting, and it blends right in.
If you'd like to make your own swords, I've uploaded the files I made to Thingiverse.
Here's the Dread Pirate Roberts Pommel: https://www.thingiverse.com/thing:3114815
And here's the Inigo Montoya guard: https://www.thingiverse.com/thing:3054622
Subscribe to:
Posts (Atom)